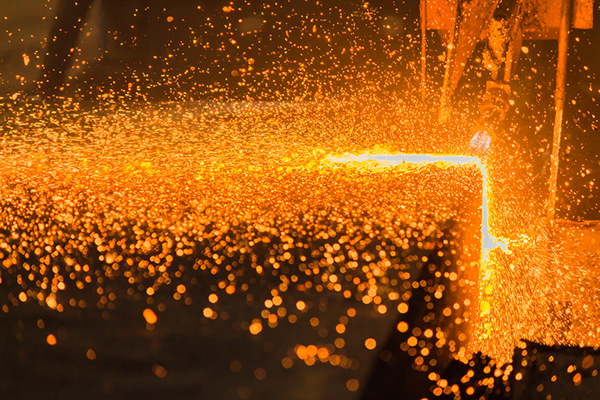
Our technology platform is broad in scope and affords the ability to produce a wide range of material for a wide range of applications.
Applications
Many applications in aerospace, energy, and industrial markets require the production of refractory metals and alloys. Conventional production techniques involve casting ingots of the starting metals, working these ingots to produce the correct form factor of each metal, followed frequently by further steps to shape the final product with significant yield loss. Alloying involves the added complexity of combining via high temperature melting the alloy components, prior to final product shaping and machining. These production techniques are lengthy, capital and energy intensive, and typically operate at low overall yield to final product.
With our patented technology, we offer a direct route to metals and alloys through one-step production of powders with the desired chemical composition, followed by densification of the powder to a finished rough shape. Lead times can be dramatically shortened, batch sizes substantially reduced, energy intensity reduced, and waste from machining minimized.
Our powders are produced as aggregates and exhibit a high degree of structure, as well as controllable internal porosity. These attributes make them well suited for techniques such as cold spray deposition, conventional metal injection molding, and other forms of powder metallurgy. While for additive layer manufacturing (“3D printing”), it may preferable first to convert our powders to spherical particles with no residual porosity, this is something we can readily achieve at high process yield, at the same time delivering a narrow size distribution of useful spherical particles.
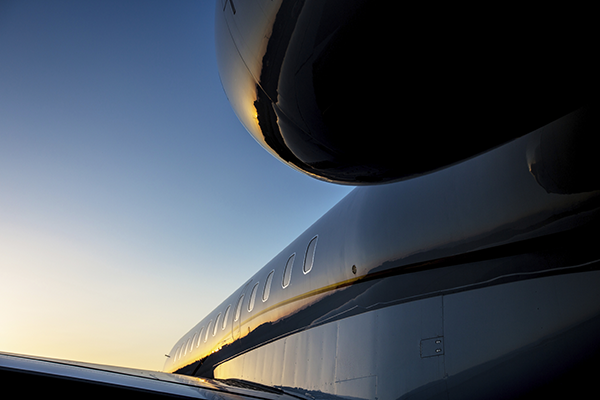
Aerospace
Titanium alloys possess numerous superior properties, including high strength-to-weight ratio, corrosion resistance, and elevated temperature performance, make these materials ideal for a wide range of applications within the aerospace industry. Indeed, aerospace is the largest single market for titanium.
Within aerospace, titanium alloys find their most significant application in turbine engines, particularly in the compressor and fan sections in such parts as inlet guide vanes, blades, and discs. However, there are many other uses of titanium, including airframes, fasteners, and landing gear.
Hafnium metal is an important alloy additive in third generation nickel-based superalloys for single crystal turbine blades.

Medical
Titanium and titanium alloys exhibit outstanding bio-compatibility, leading to their use in many biomedical applications where rejection might otherwise be a concern. The mechanical properties of titanium alloys are well matched to bone, permitting their use in load-bearing implants, and their corrosion resistance means they remain functionally effective for many years. In addition, careful preparation of bone-facing surfaces on titanium implants (for example by powder-coating or roughening the implant surface to create porosity) permits rapid and durable bone in-growth, helping integrate the implants and providing better long term outcomes for patients.
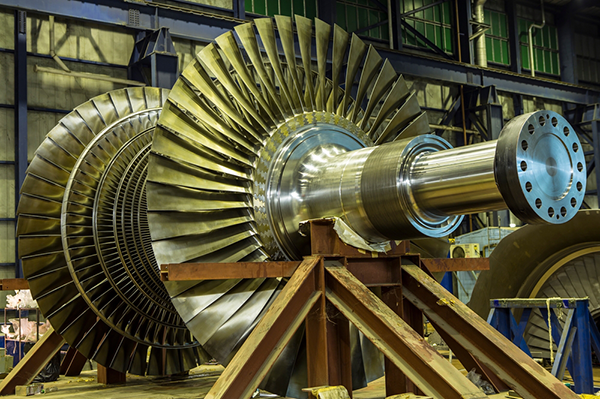
Energy
Hafnium metal is an important alloying element for second-generation nickel-based superalloys deployed in land-based gas turbines. Hafnium is found in the directionally solidified turbine blades that comprise these turbines.
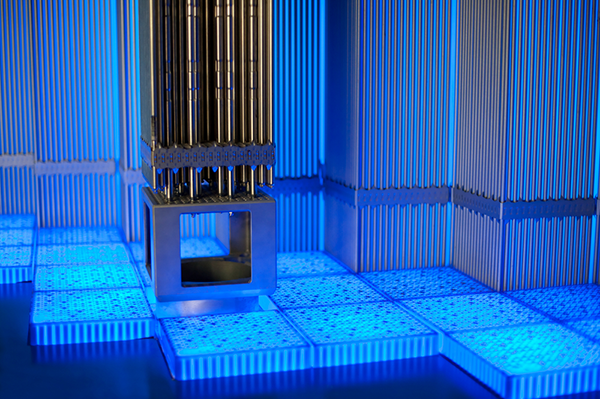
Nuclear
Hafnium has a high neutron absorption cross section, which has led to hafnium being used in control rods to regulate nuclear reactors. The control rods are positioned within the reactor core, and their positions are then adjusted to modulate the rate at which nuclear fission occurs.
Titanium has numerous applications in the nuclear field, including condenser tubing for selected water and steam systems, as well as in disposal systems.
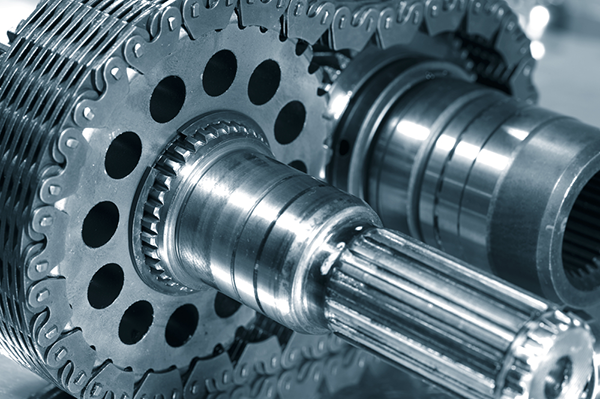
Other
Titanium has a wide range of other industrial uses, including in chemical processing plants, desalination plants, high-performance engine components, and transportation. Titanium is also common in military systems thanks to its high strength-to-weight ratio.
Hafnium metal is also used as consumable electrode tips in plasma cutting systems, because of its ability to operate in oxygen-rich atmospheres, and in some applications (as the oxide) within electronics.